The Complete Guide to Sandwich Panel Production Lines
Introduction to Sandwich Panel Production Technology
Sandwich panels have revolutionized the construction, refrigeration, and industrial building sectors by offering superior insulation properties, structural integrity, and ease of installation. These versatile building components consist of two metal facings with an insulating core material sandwiched between them. The manufacturing of these panels relies on sophisticated production lines that ensure consistent quality, precise dimensions, and optimal bonding between layers.
This comprehensive guide explores the intricate world of sandwich panel production lines, covering their working principles, various types based on core materials, key components, diverse applications, and critical factors to consider when investing in this technology. Whether you’re a manufacturer looking to expand your production capabilities, an investor researching market opportunities, or a construction professional seeking to understand the manufacturing process behind these essential building materials, this guide provides valuable insights into sandwich panel production technology.
Working Principles of Sandwich Panel Production Lines
Sandwich panel production lines operate on a continuous manufacturing principle that transforms raw materials into finished panels through a series of synchronized processes. Understanding these fundamental principles is essential for anyone involved in the manufacturing, purchasing, or specification of sandwich panels.
Basic Production Flow and Process Stages
The sandwich panel production process follows a logical sequence that ensures efficient manufacturing and consistent quality. While specific details may vary between different types of production lines, the fundamental stages remain consistent:
1.Raw Material Preparation:
The process begins with the preparation of the metal facings (typically steel or aluminum coils) and the core material (PU, PIR, EPS, mineral wool, etc.).
2.Decoiling and Sheet Feeding:
Metal coils are loaded onto decoilers, which feed the sheet material into the production line at a controlled rate.
3.Surface Treatment and Preparation:
The metal sheets undergo cleaning, degreasing, and sometimes primer application to ensure optimal adhesion with the core material.
4.Core Material Processing:
Depending on the type of panel being produced, the core material is either prepared in sheet form (for EPS, mineral wool) or as liquid components (for PU/PIR foam systems).
5.Assembly and Bonding:
The core material is positioned between the prepared metal facings, creating the sandwich structure.
6.Pressing and Curing:
The assembled layers pass through a continuous press where heat and pressure are applied to ensure proper bonding and curing of adhesives or foam systems.
7.Cutting and Finishing:
The continuous panel is cut to specified lengths using precision cutting systems, and edge finishing may be applied.
8.Quality Control and Packaging:
Finished panels undergo inspection for dimensional accuracy, bond strength, and surface quality before being packaged for shipping.
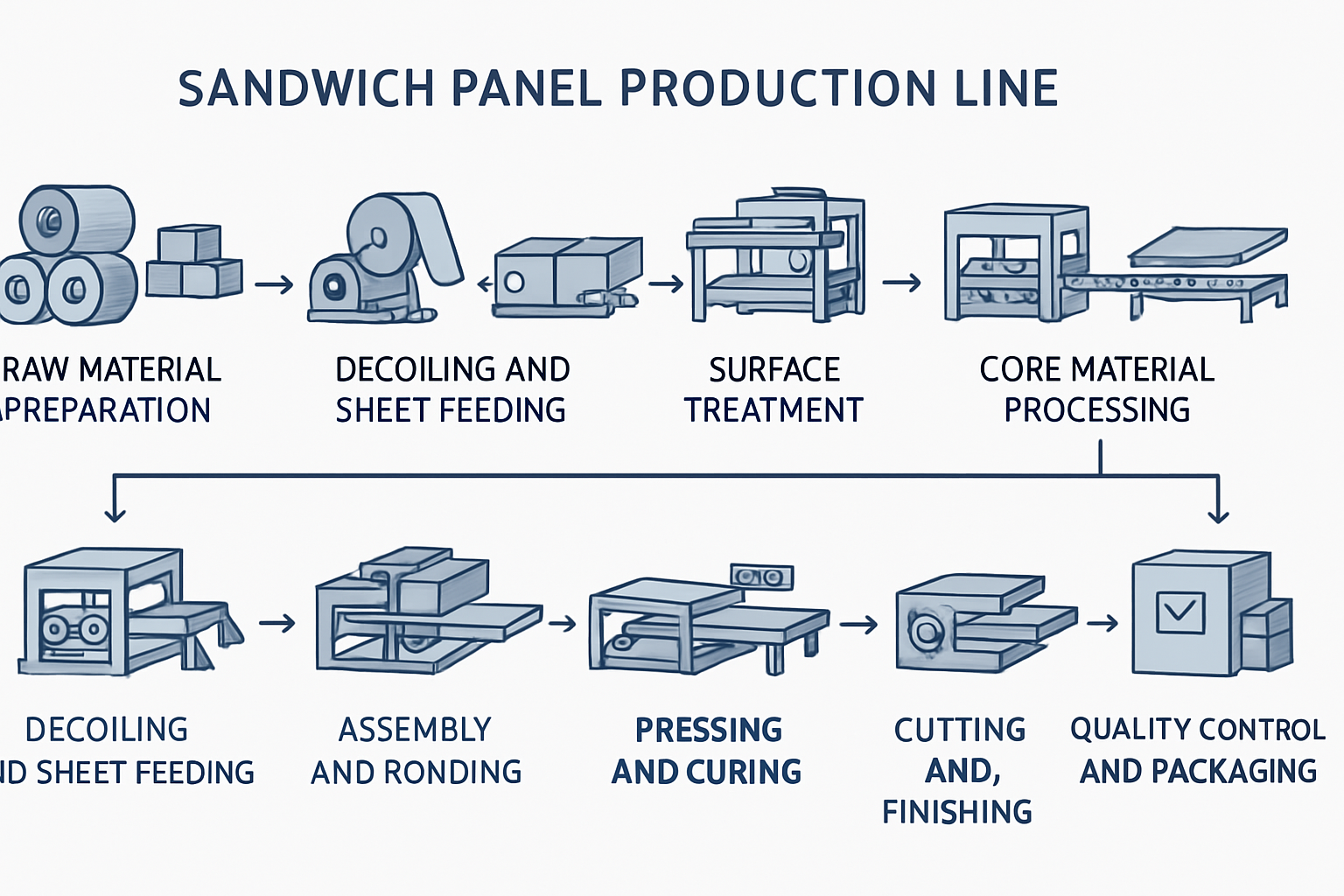
Sandwich Panel Production Line Process Flow
Figure 1: Diagram illustrating the typical process flow of a sandwich panel production line, from raw material preparation to finished panel packaging.
Continuous vs. Discontinuous Production Methods
Sandwich panel production lines can be categorized into two main operational methods, each with distinct advantages and applications:
Continuous Production Lines:
- Feature uninterrupted production flow from start to finish - Higher production capacity (typically 800-2,500 m² per hour) - Greater automation and reduced labor requirements - Suitable for large-scale manufacturing and standardized panel specifications - Higher initial investment but lower per-unit production costs - Examples include continuous PU/PIR lines and high-capacity mineral wool panel lines
Discontinuous Production Lines:
- Operate in batch processing mode rather than continuous flow - Lower production capacity (typically 200-600 m² per hour) - More flexibility for producing custom panel sizes and specifications - Lower initial investment cost, making them suitable for smaller manufacturers - Higher per-unit production costs due to increased labor requirements - Examples include discontinuous EPS panel lines and small-scale production systems
Production Method | Capacity (m²/hour) | Initial Investment | Labor Requirements | Flexibility | Best For |
Continuous | 800-2,500 | High | Low | Limited | Large-scale, standardized production |
Discontinuous | 200-600 | Medium | Medium-High | High | Small-scale, customized production |
Table 1: Comparison of continuous and discontinuous sandwich panel production methods
Manufacturer of PU sandwich panel line.One machine can make both Pu roof and wall panel automatically & continuously.
EPS sandwich panel Production line of Zhongyuan factory can automatically and continuously manufacture EPS roof and wallboard.
One machine can make both PU sandwich panel forming machine automatically & continuously.
Key Technical Parameters and Performance Metrics
Several critical technical parameters determine the performance and capabilities of sandwich panel production lines:
•Production Speed: Measured in meters per minute or square meters per hour
•Panel Thickness Range: Minimum and maximum panel thickness capabilities
•Panel Width Range: Minimum and maximum panel width capabilities
•Core Material Compatibility: Types of core materials the line can process
•Facing Material Compatibility: Types and thicknesses of metal facings the line can handle
•Energy Consumption: Power requirements per unit of production
•Automation Level: Degree of automated operation vs. manual intervention required
•Quality Control Systems: Integrated inspection and quality assurance capabilities
Understanding these parameters is essential when evaluating different production lines and determining which system best meets specific manufacturing requirements.
Types of Sandwich Panel Production Lines by Core Material
Sandwich panel production lines are primarily categorized by the type of core material they process. Each core material requires specific processing equipment and techniques to achieve optimal panel quality and performance.
Polyurethane (PU) and Polyisocyanurate (PIR) Panel Lines
PU/PIR sandwich panel production lines are among the most common and versatile systems in the industry. These lines produce panels with excellent thermal insulation properties, making them ideal for cold storage facilities, refrigerated transport, and energy-efficient buildings.
Key Features:
- Liquid two-component chemical system (polyol and isocyanate) that reacts to form rigid foam - High-pressure mixing and dispensing systems for precise foam formulation - Temperature-controlled double belt press for foam expansion and curing - Advanced chemical metering systems for consistent foam quality - Typical thermal conductivity of finished panels: 0.022-0.028 W/mK
Production Process Specifics:
1. The two chemical components are stored in temperature-controlled tanks
2. A high-pressure mixing head combines the components in precise ratios
3. The mixed chemicals are dispensed onto the lower metal facing
4. The upper metal facing is applied, and the assembly enters the double belt press
5. Heat is applied to accelerate the chemical reaction and foam expansion
6. The continuous panel is cured under controlled pressure and temperature
7. The cured panel is cut to length and edge-finished
Applications:
- Cold storage facilities and refrigerated warehouses
- Food processing facilities
- Controlled atmosphere storage
- Clean rooms and pharmaceutical facilities
- Commercial and residential buildings requiring high insulation values
Expanded Polystyrene (EPS) Panel Lines
EPS sandwich panel production lines manufacture panels with a pre-formed expanded polystyrene core. These panels offer a good balance of insulation properties and cost-effectiveness, making them popular for general construction applications.
Key Features:
- Uses pre-formed EPS boards as the core material - Adhesive application systems for bonding EPS to metal facings - Typically lower investment cost compared to PU/PIR lines - Simpler production process with fewer chemical handling requirements - Typical thermal conductivity of finished panels: 0.035-0.040 W/mK
Production Process Specifics:
1. Pre-cut EPS boards are fed into the production line
2. Adhesive is applied to both sides of the EPS boards
3. Metal facings are positioned on both sides of the adhesive-coated EPS
4. The assembly passes through a press that applies pressure for bonding
5. The bonded panel is cured and then cut to the required length
Applications:
- General building construction
- Partition walls and interior applications
- Agricultural buildings
- Temporary structures and modular buildings
- Budget-conscious projects with moderate insulation requirements
Mineral Wool and Rock Wool Panel Lines
Mineral wool and rock wool panel production lines manufacture panels with superior fire resistance and acoustic properties. These panels are essential for applications where fire safety is a critical requirement.
Key Features:
- Uses mineral wool or rock wool slabs as the core material
- Specialized handling systems for the fibrous core material
- Fire-resistant adhesive application systems
- Typically higher production line cost due to complex material handling
- Typical thermal conductivity of finished panels: 0.035-0.045 W/mK - Superior fire resistance (typically A1 or A2 fire classification)
Production Process Specifics:
1. Mineral wool slabs are cut to the required dimensions
2. Fire-resistant adhesive is applied to both sides of the mineral wool
3. Metal facings are positioned on both sides of the adhesive-coated mineral wool
4. The assembly passes through a press that applies controlled pressure
5. The bonded panel is cured and then cut to the required length
6. Edge finishing may include specialized sealing for moisture resistance
Applications:
- Fire-rated building partitions and walls
- Industrial facilities with high fire safety requirements
- Power plants and high-risk facilities
- Buildings requiring acoustic insulation
- Marine and offshore applications
Glass Wool Core Panel Lines
HGlass wool core panel production lines create lightweight panels with good thermal and acoustic properties. These panels are less common but offer specific advantages for certain applications.
Key Features:
- Uses glass wool batts or boards as the core material
- Specialized handling systems for the delicate core material
- Good balance of thermal and acoustic properties
- Typically lighter weight than mineral wool panels
- Typical thermal conductivity of finished panels: 0.032-0.040 W/mK
Production Process Specifics:
Similar to mineral wool panel production but with specialized handling for the more delicate glass wool material.
Applications:
- Acoustic ceiling and wall panels
- HVAC ductwork and enclosures
- Lightweight construction applications
- Projects requiring balanced thermal and acoustic performance
Key Components and Equipment in Sandwich Panel Production Lines
A sandwich panel production line consists of several specialized machines and systems working in coordination to transform raw materials into finished panels. Understanding these components is essential for evaluating production line capabilities and maintenance requirements.
Material Handling and Preparation Systems
The initial stage of the production line involves systems for handling and preparing the raw materials:
Decoiling and Sheet Feeding Systems:
- Hydraulic or motorized decoilers for metal coil handling
- Coil loading cars for efficient coil changes
- Sheet guiding and alignment systems
- Sheet cleaning and degreasing units
- Accumulation loops to maintain continuous operation during coil changes
Core Material Preparation Systems:
- For PU/PIR: Temperature-controlled storage tanks, pumping systems, and mixing units
- For EPS/Mineral Wool: Core sheet feeding and positioning systems
- Adhesive preparation and application systems
- Core material cutting and sizing equipment
Panel Formation and Pressing Equipment
The heart of the production line where the sandwich structure is formed and bonded:
Double Belt Press (for PU/PIR lines):
- Temperature-controlled upper and lower belts
- Precise gap control systems for panel thickness
- Heating and cooling zones for optimal foam curing
- Drive systems with speed control for production rate adjustment
Lamination Press (for EPS/Mineral Wool lines):
- Continuous or discontinuous pressing systems
- Pressure control systems for optimal bonding
- Heating elements for adhesive curing
- Conveyor systems for panel transport
Profiling and Forming Equipment:
- Edge forming systems for joint designs (tongue and groove, lap joint, etc.)
- Profile roll forming units for specialized panel edges
- Embossing systems for surface texturing (if required)
Cutting and Finishing Systems
Equipment that transforms the continuous panel into finished products:
Cutting Systems:
- Flying saw or stop-and-cut systems for precise length cutting
- Cross-cutting and longitudinal cutting capabilities
- Automated dimension control systems
- Waste handling and recycling systems
Finishing Equipment:
- Edge finishing and sealing systems
- Surface cleaning and inspection stations
- Defect marking systems
- Stacking and packaging equipment
Control and Automation Systems
Modern sandwich panel production lines rely heavily on advanced control systems:
Central Control System:
- PLC (Programmable Logic Controller) or industrial PC
-based control
- HMI (Human-Machine Interface) for operator interaction
- Recipe management for different panel specifications
- Production data logging and reporting
Quality Control Systems:
- Thickness measurement sensors
- Surface inspection cameras
- Bond strength testing equipment
- Thermal performance testing
Safety Systems:
- Emergency stop circuits
- Safety light curtains and barriers
- Lockout/tagout systems
- Chemical handling safety systems (for PU/PIR lines)
Applications and Industries Served by Sandwich Panels
Sandwich panels manufactured on these production lines serve diverse applications across multiple industries, each with specific requirements and performance expectations.
Cold Storage and Refrigeration Facilities
One of the primary applications for sandwich panels, particularly those with PU/PIR cores:
•Walk-in coolers and freezers
•Large-scale cold storage warehouses
•Food processing facilities
•Pharmaceutical storage
•Temperature-controlled logistics centers
These applications require panels with:
- Excellent thermal insulation (low U-values)
- Vapor barriers to prevent moisture migration
- Food-safe surface finishes
- Resistance to temperature cycling
- Airtight joint systems
Commercial and Industrial Buildings
Sandwich panels are widely used in modern commercial and industrial construction:
•Warehouse and factory walls and roofs
•Retail buildings and supermarkets
•Agricultural buildings and storage facilities
•Office buildings and commercial centers
•Sports facilities and exhibition halls
These applications typically require:
- Good thermal performance
- Weather resistance
- Aesthetic appearance options
- Cost-effective installation
- Durability and low maintenance
Clean Rooms and Controlled Environments
Specialized sandwich panels serve critical controlled environment applications:
•Pharmaceutical manufacturing facilities
•Semiconductor production facilities
•Food processing clean rooms
•Healthcare facilities
•Laboratory environments
These demanding applications require panels with:
- Non-particulating surfaces
- Chemical resistance
- Easy cleaning and disinfection
- Airtight sealing systems
- Controlled electrostatic properties
Modular and Prefabricated Construction
The growing modular construction sector relies heavily on sandwich panels:
•Prefabricated building modules
•Temporary and relocatable buildings
•Disaster relief shelters
•Military and remote site facilities
•Construction site offices and facilities
These applications benefit from:
- Lightweight construction
- Rapid assembly
- Transportability
- Reusability
- Integrated structural and insulation properties
Purchasing Considerations and Investment Analysis
Investing in a sandwich panel production line represents a significant capital expenditure that requires careful consideration of multiple factors.
Production Capacity Planning and Market Analysis
Before selecting a production line, thorough market analysis and capacity planning are essential:
Market Assessment Factors:
- Local and regional demand for sandwich panels
- Competitive landscape and market saturation
- Price points and profit margins
- Market growth projections
- Export opportunities
Capacity Planning Considerations:
- Initial production volume requirements
- Growth projections and scalability needs
- Seasonal demand fluctuations
- Product mix and changeover requirements
- Maintenance downtime allowances
A production line operating at optimal capacity will provide the best return on investment, while overcapacity leads to inefficiency and undercapacity limits growth potential.
Total Cost of Ownership Analysis
The true cost of a sandwich panel production line extends far beyond the initial purchase price:
Initial Investment Components:
- Base machinery and equipment
- Customization and special features
- Installation and commissioning
- Training and startup support
- Facility modifications and infrastructure
Ongoing Operational Costs:
- Energy consumption
- Raw material usage and waste
- Labor requirements
- Maintenance and spare parts
- Consumables and supplies
Long-term Considerations:
- Equipment lifespan and depreciation
- Upgrade pathways and future compatibility
- Resale value
- Productivity improvements over time
- Technology obsolescence risks
A comprehensive TCO analysis should cover at least a 10-year operational period to accurately assess the investment value.
Technical Specifications and Customization Options
Production lines should be specified to meet both current and future manufacturing requirements:
Core Technical Specifications:
- Production capacity (m²/hour)
- Panel thickness range
- Panel width capabilities
- Core material compatibility
- Facing material options
- Energy consumption
- Space requirements
Customization Considerations:
- Special profile and joint designs
- Surface finishing options
- Integrated quality control systems
- Automation level
- Industry
-specific requirements
Future-proofing Features:
- Modular design for capacity expansion
- Flexibility for new product development
- Compatibility with emerging materials
- Upgrade pathways for control systems
- Energy efficiency improvements
Supplier Evaluation and Support Services
The relationship with the production line supplier extends far beyond the initial purchase:
Supplier Evaluation Criteria:
- Industry reputation and track record
- Installed base and reference customers
- Financial stability and longevity
- Global presence and local support
- R&D investment and innovation history
Critical Support Services:
- Installation and commissioning
- Operator and maintenance training
- Spare parts availability and delivery
- Technical support and troubleshooting
- Software updates and improvements
Partnership Considerations:
- Technology transfer and knowledge sharing
- Continuous improvement programs
- Joint product development opportunities
- Market intelligence sharing
- Long-term relationship potential
Selecting a supplier with strong support capabilities can significantly impact the success of the investment and ongoing operations.
Future Trends and Innovations in Sandwich Panel Production
The sandwich panel production industry continues to evolve with technological advancements and changing market demands.
Automation and Industry 4.0 Integration
Modern production lines are increasingly incorporating advanced automation and Industry 4.0 concepts:
•Fully automated material handling and logistics
•Real-time production monitoring and analytics
•Predictive maintenance systems
•Digital twin technology for process optimization
•Remote monitoring and support capabilities
•AI-driven quality control and defect detection
These technologies improve efficiency, reduce waste, and minimize downtime while providing valuable data for continuous improvement.
Sustainability and Environmental Considerations
Environmental concerns are driving significant changes in sandwich panel production:
•Low-GWP (Global Warming Potential) blowing agents for PU/PIR foams
•Recycled content in metal facings and core materials
•Energy-efficient production processes
•Waste reduction and recycling systems
•Life cycle assessment and environmental product declarations
•Circular economy approaches to panel end-of-life
Manufacturers investing in new production lines should consider these sustainability factors not only for environmental responsibility but also for future regulatory compliance and market acceptance.
Advanced Materials and Performance Enhancements
Research and development continue to improve panel performance through material innovations:
•Nano-enhanced insulation materials
•Bio-based foam systems
•Self-healing coatings and surfaces
•Phase-change materials for thermal management
•Integrated photovoltaic and energy-harvesting capabilities
•Smart panels with embedded sensors and monitoring
Production lines with the flexibility to incorporate these emerging materials will maintain competitive advantage as the market evolves.
Conclusion and Key Takeaways
Sandwich panel production lines represent a significant but potentially rewarding investment for manufacturers serving the construction and industrial building sectors. The technology continues to advance, offering improved efficiency, product performance, and sustainability.
Key considerations for potential investors include:
1.Thorough market analysis to determine demand, competition, and growth potential
2.Careful matching of production capacity to market requirements
3.Comprehensive evaluation of total cost of ownership, not just initial investment
4.Selection of appropriate core material technology based on target applications
5.Consideration of future trends in automation, sustainability, and materials
6.Development of strong supplier relationships for ongoing support and innovation
With proper planning, specification, and management, a sandwich panel production line can provide a strong foundation for a successful manufacturing business serving the evolving needs of the construction industry.